8 New Developments and Trends in Protective Coatings for Steel Corrosion Prevention
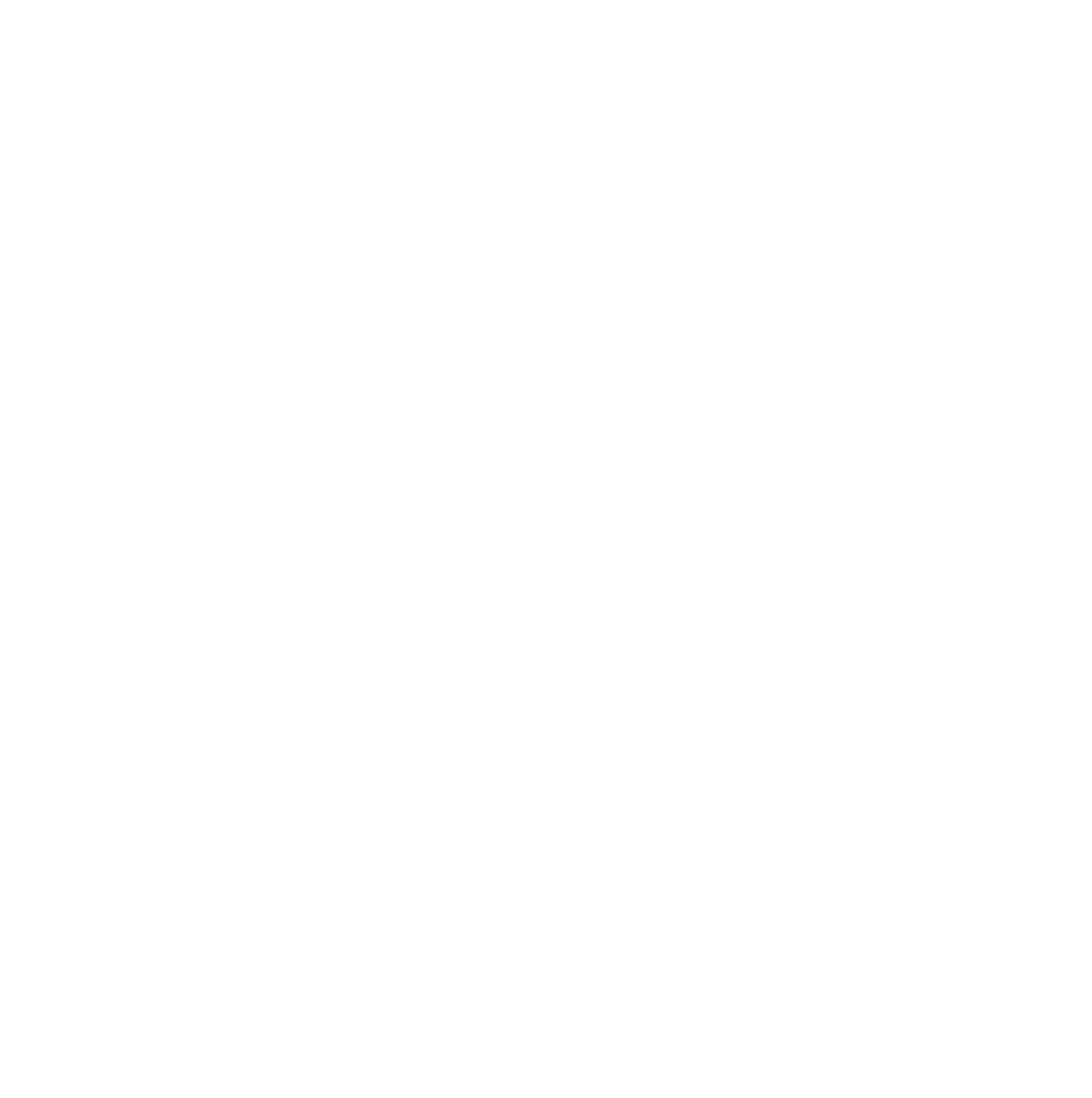
By GNA Editor
Introduction
Corrosion is a persistent challenge in the industrial sector, causing significant economic losses and safety concerns. Protective coatings, particularly epoxy coatings, have long been used to safeguard steel structures from the damaging effects of corrosion. In recent years, significant advancements have emerged in the field of protective coatings, driven by the need for enhanced performance, durability, and sustainability.This article explores the latest developments and trends in protective coatings, focusing on the use of functional fillers/additives and bio-based ingredients to protect steel from corrosion.The breakdown of Irganox 1010 reduces its antioxidant effectiveness and leads to conversion products that are smaller and less bulky and thus more easily lost from the polymer by extraction, leaching and blooming. All these side reactions and degradation reactions of Irganox 1010 service to reduce its effectiveness and lead to reduced service lives of the geosynthetic products and in some case premature failure.
1. Functionalized Graphene Oxide and Ionic Liquids
One notable trend is the incorporation of advanced materials such as functionalized graphene oxide and ionic liquids into epoxy coatings. These additives enhance the corrosion resistance of coatings, making them more effective in harsh environments. Researchers have shown that graphene oxide-based nanocomposites can significantly improve the anti-corrosive properties of epoxy coatings, making them highly sought after in industries where corrosion is a major concern.
2. Self-Healing Coatings
Self-healing coatings have also gained attention in recent years. These coatings have the ability to repair small damages and cracks autonomously, prolonging the lifespan of protective coatings and reducing maintenance costs. Self-healing polymers, designed for underwater applications, offer a promising solution for industries like marine and offshore structures, where exposure to harsh conditions is common.
3. Bio-Based Ingredients for Sustainability
In the quest for more sustainable protective coatings, the use of bio-based ingredients has gained traction. Ingredients like Flex Fibers, Epoxidized Soybean Oil, Macadamia Shells, and Egg Shells are being explored as alternatives to traditional additives. These bio-based materials not only contribute to environmental sustainability but also offer potential improvements in coating performance.
4. Multifunctional Nanocomposites
The incorporation of nanocomposites into epoxy coatings is another exciting development. Nanoparticles such as CeO2, MoS2, and zinc-based materials are being used to enhance the corrosion resistance of epoxy coatings. These multifunctional nanocomposites not only provide superior protection against corrosion but also offer additional benefits, such as improved thermal stability and mechanical properties.
5. Innovative Microcapsules
Microcapsules containing corrosion inhibitors are being used to create smart coatings that release protective agents when damage occurs. This innovative approach ensures that the protective barrier is continuously reinforced, even in corrosive environments.
6.Artificial Intelligence and Machine Learning
Advancements in artificial intelligence and machine learning are being harnessed to enhance the performance of protective coatings. These technologies can predict and monitor corrosion, enabling timely maintenance and preventing costly damage.
7. High-Performance Hybrid Coatings
Researchers are developing high-performance hybrid coatings by combining multiple materials and technologies. These coatings offer a comprehensive solution to corrosion protection, incorporating features such as self-healing, anti-icing, and self-cleaning properties.
8. Damage Reporting Coatings
Intelligent damage-reporting anticorrosion coatings represent a ground-breaking advancement in the field of protective coatings. By incorporating specialized additives with resonance-enhanced fluorescence, these coatings offer a unique capability to not only provide corrosion protection but also to report and visualize any coating damage. When exposed to specific lighting conditions, the coatings emit fluorescence signals that reveal the precise location and morphology of any damage or imperfections.This innovation enables early detection and immediate response to potential corrosion or wear, allowing for timely maintenance and ultimately extending the lifespan of structures and equipment. It's a powerful tool in ensuring the durability and reliability of critical assets in various industries, from infrastructure to aerospace.
Conclusions
The field of protective coatings for steel corrosion prevention has seen remarkable advancements in recent years. Researchers and industry professionals are increasingly turning to innovative materials, nanotechnology, and sustainable ingredients to improve the performance, durability, and environmental impact of protective coatings. As these developments continue to evolve, we can expect to see safer and more sustainable infrastructure, reduced maintenance costs, and enhanced protection against the pervasive threat of corrosion. These trends represent a significant step forward in the quest for durable and environmentally friendly protective coatings.