Will your product stand up to the weathering elements?
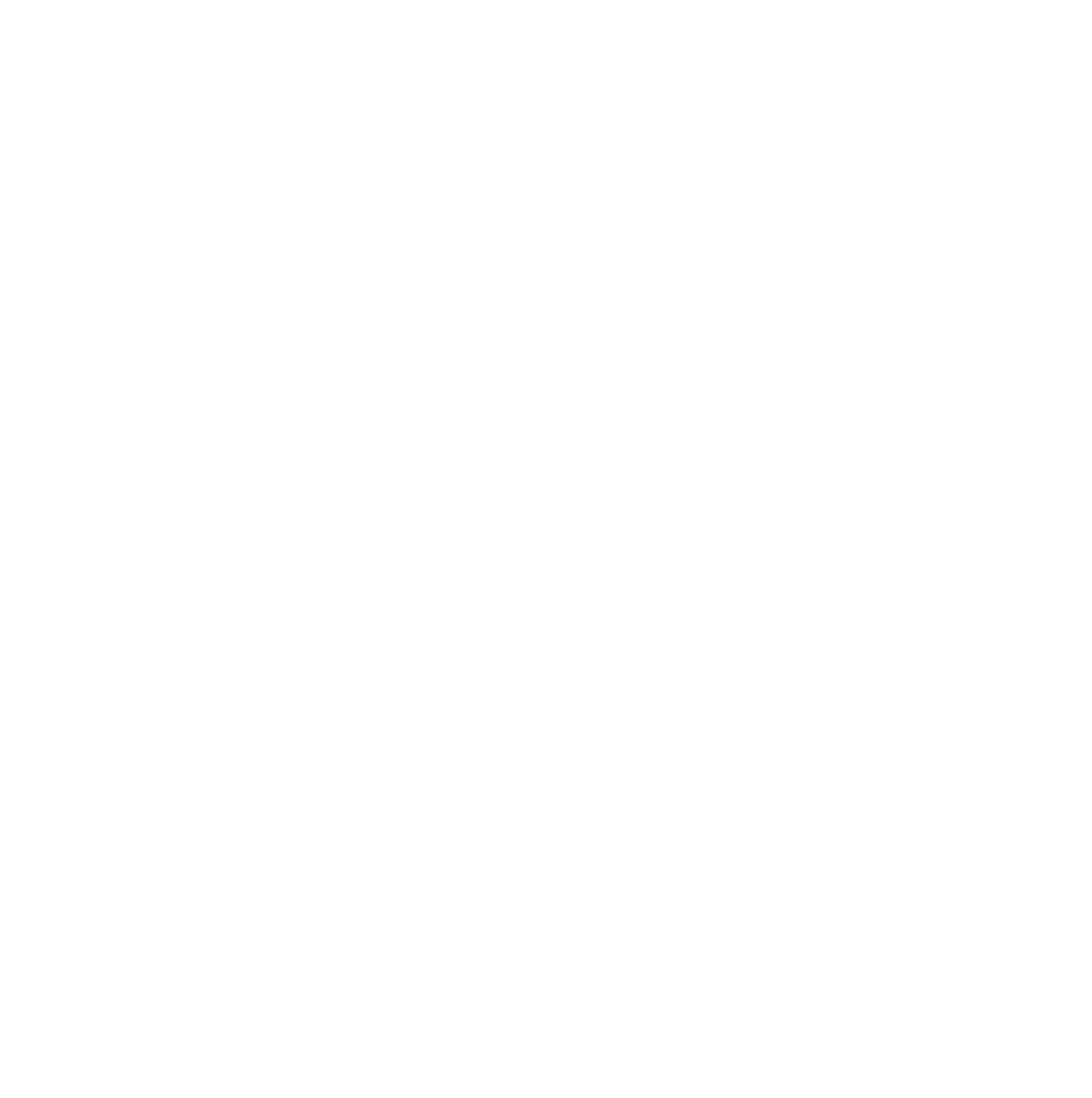
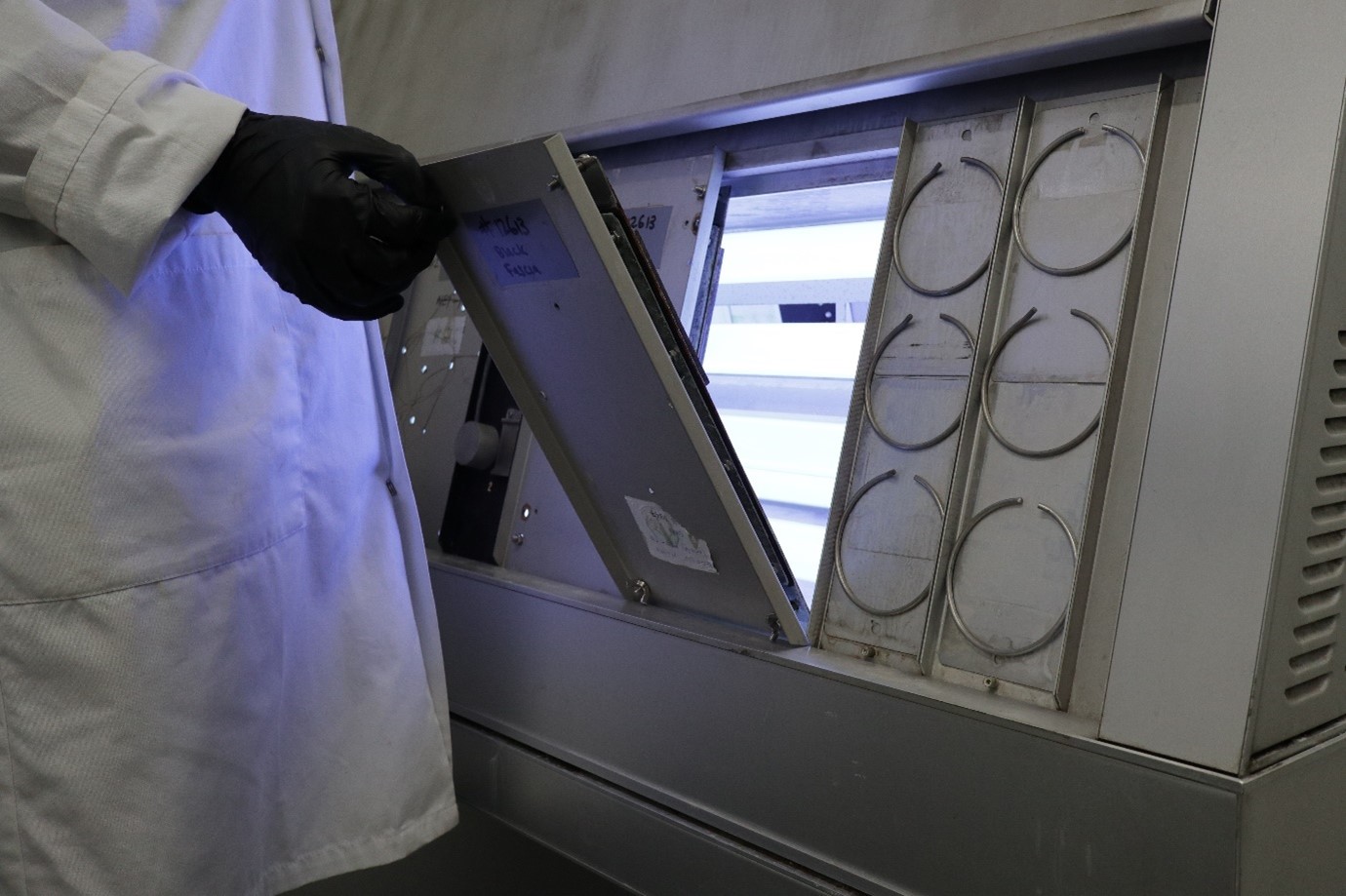
Understanding UV-Induced Degradation
Exposure to ultraviolet (UV) radiation, heat, and moisture leads to material degradation over time. This degradation, known as photo-oxidation, compromises structural integrity and performance, resulting in issues such as cracking, embrittlement, chalking, fading, and reduced mechanical properties.
At ExcelPlas, we conduct Accelerated UV Weathering (QUV) Testing to simulate and evaluate long-term material durability. By accelerating environmental exposure in a controlled setting, we provide critical insights into material resilience and expected service life.
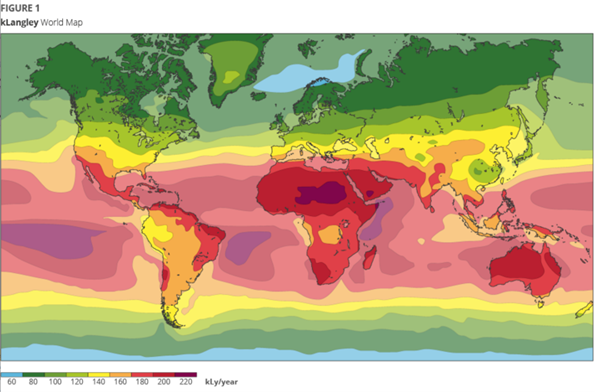
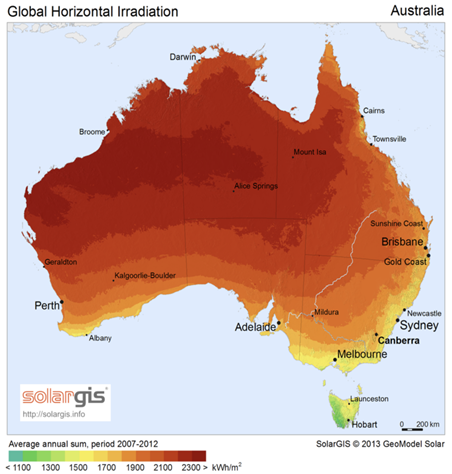
QUV Testing Methodology
Our QUV testing chambers expose materials to precisely controlled cycles of UV radiation, temperature, and moisture, replicating real-world weathering conditions in an accelerated timeframe.
- Fluorescent UV Lamps (UVA-340 or UVB-313) provide controlled UV exposure.
- Thermal Cycling & Humidity Control mimic outdoor temperature fluctuations.
- Condensation & Drying Phases replicate dew and rainfall conditions.
This systematic approach enables accurate prediction of material performance, allowing for timely formulation adjustments and improved product reliability.
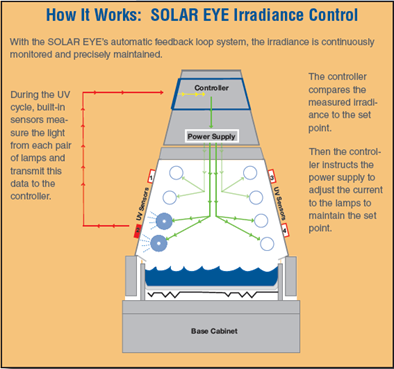
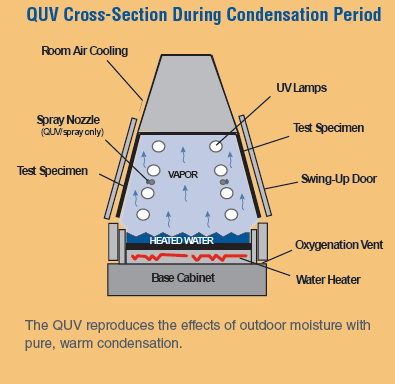
Compliance with Industry Standards
ExcelPlas adheres to internationally recognized testing protocols, ensuring reliable and repeatable results. Our QUV testing meets the requirements of:
- ASTM G154 – Standard practice for UV exposure of non-metallic materials
- ASTM D4329 – UV exposure of plastics for performance assessment
- ASTM D4587 – UV exposure of coatings for accelerated weathering
- ASTM D7238 – UV exposure of geosynthetics
- ISO 4892 – Plastics weathering testing under laboratory conditions
By aligning with these standards, we provide data that is scientifically robust and industry-recognized, ensuring compliance with regulatory and quality requirements.
Post-Exposure Analysis
Following QUV exposure, materials are meticulously assessed for:
- Visual and Surface Changes – Color fading, gloss loss, chalking, and surface texture alterations
- Mechanical Property Retention – Tensile strength, elongation, impact resistance, and hardness
- Structural Integrity – Crack formation, embrittlement, and adhesion failure in coatings
This detailed evaluation allows manufacturers to make informed decisions about product durability, formulation adjustments, and material suitability for specific environments.
Applications of QUV Testing
QUV testing is essential for industries where UV durability is critical:
- Polymers and Plastics – Assessing UV stability of outdoor applications
- Coatings and Paints – Evaluating weathering resistance of protective coatings
- Automotive and Aerospace – Ensuring material longevity under extreme conditions
- Construction and Infrastructure – Validating performance of building materials
- Consumer Goods and Packaging – Ensuring UV resistance for extended shelf life
ExcelPlas: Your Partner in Advanced Materials Testing
With state-of-the-art testing facilities and a commitment to precision, ExcelPlas delivers dependable, industry-leading QUV testing solutions. Our expertise ensures that your materials are rigorously evaluated under controlled conditions, providing you with the confidence to move forward in product development and compliance.
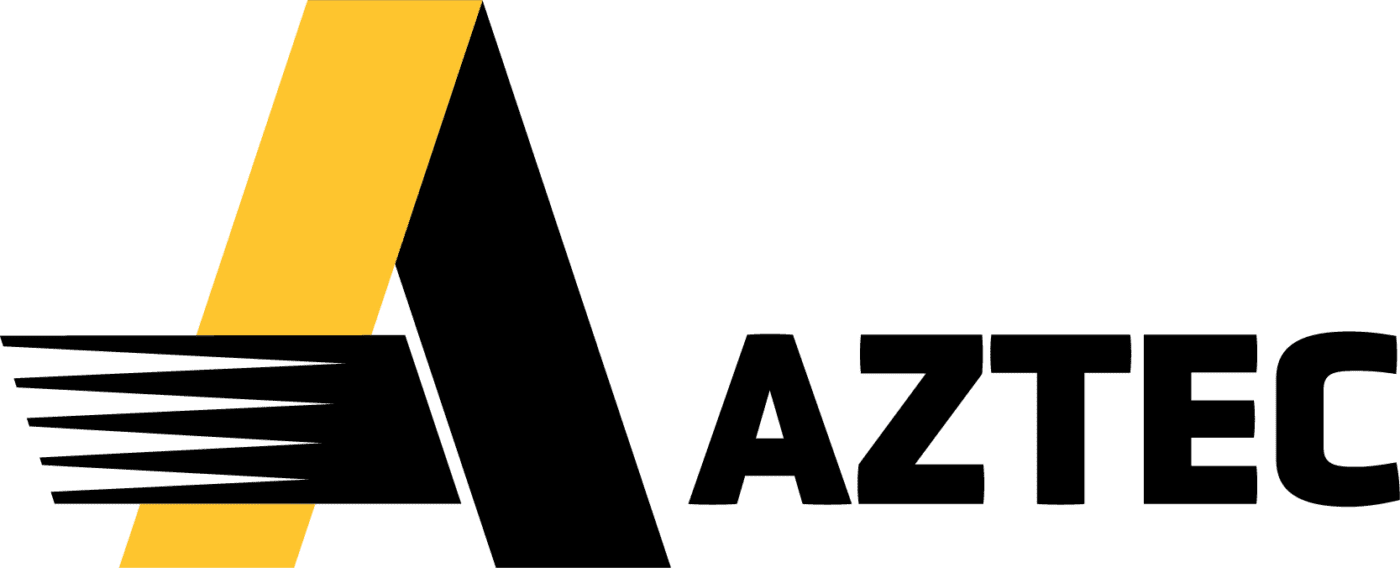
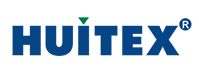
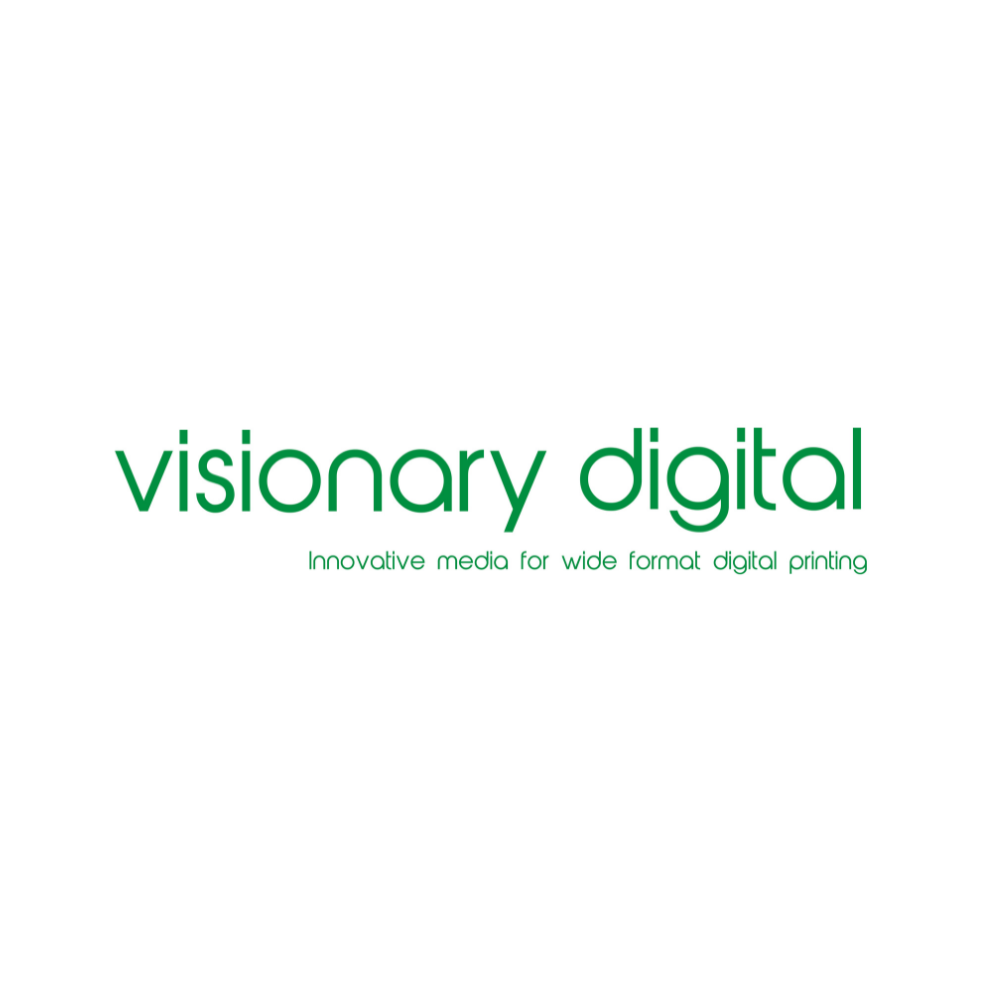
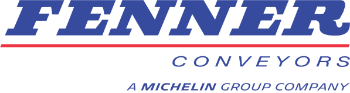
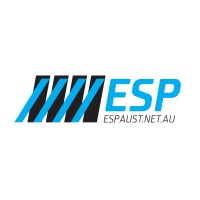
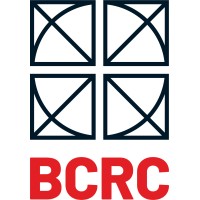
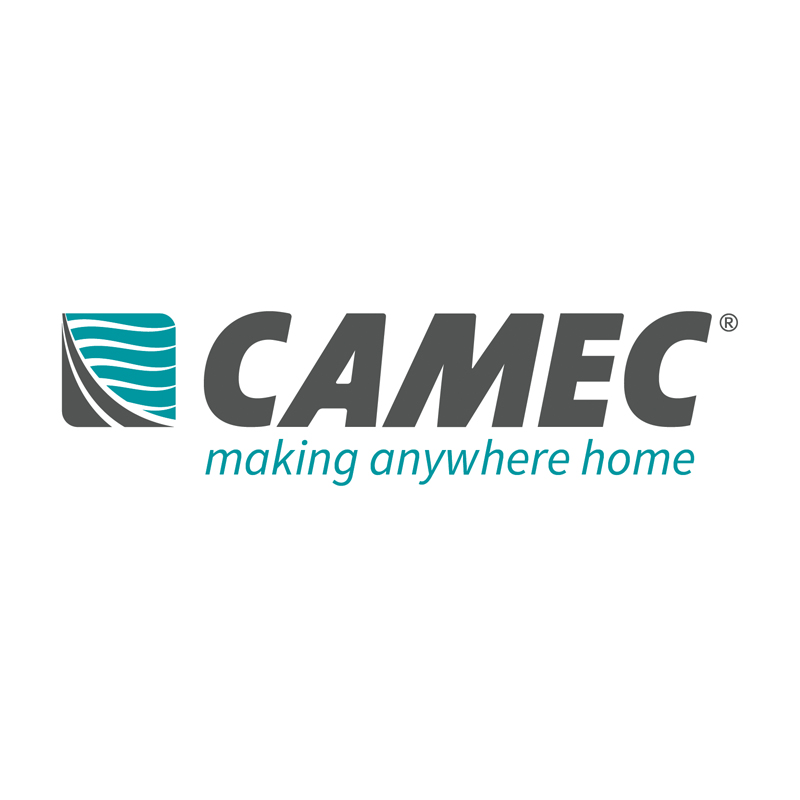
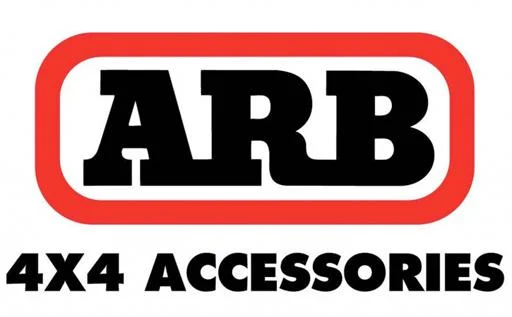
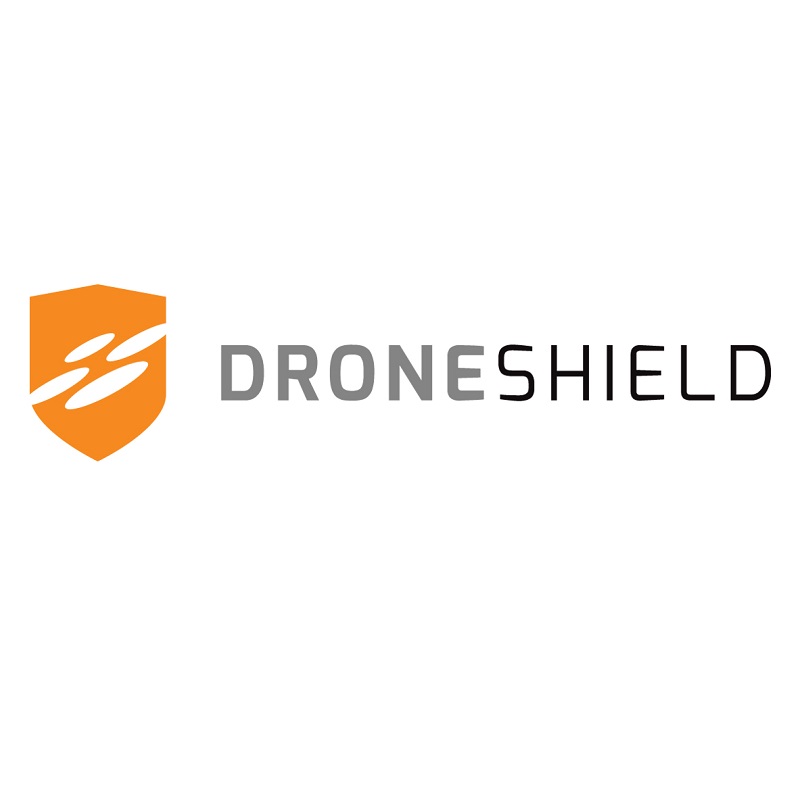
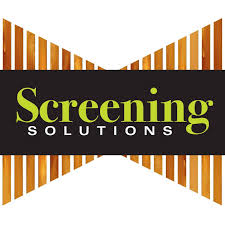
Explore in depth
Testing you can trust
Our expert team has completed over 13,000 rigorous polymer tests for clients across industries, all over the world.
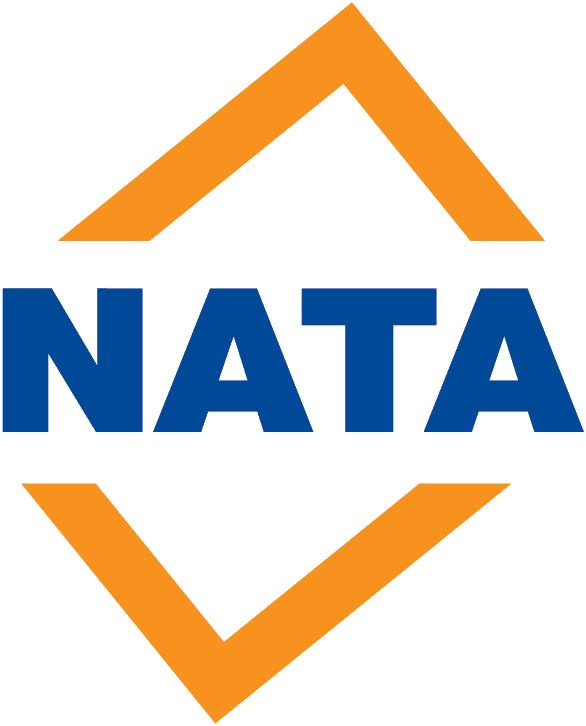
Fully independent
Audit your products quality and durability with our independent lab ensuring unbiased and accurate results from industry experts.
30+ years experience
With 30 years under our belt, ExcelPlas provides unparalleled expertise.
World class testing facilities
Equipped with a wide range of instrumentation and expertise to back it up we provide reliable and efficient testing.
Trusted by the industry
ExcelPlas’ expertise has been utilised by billion-dollar industry players relying on ExcelPlas to make the important decisions.
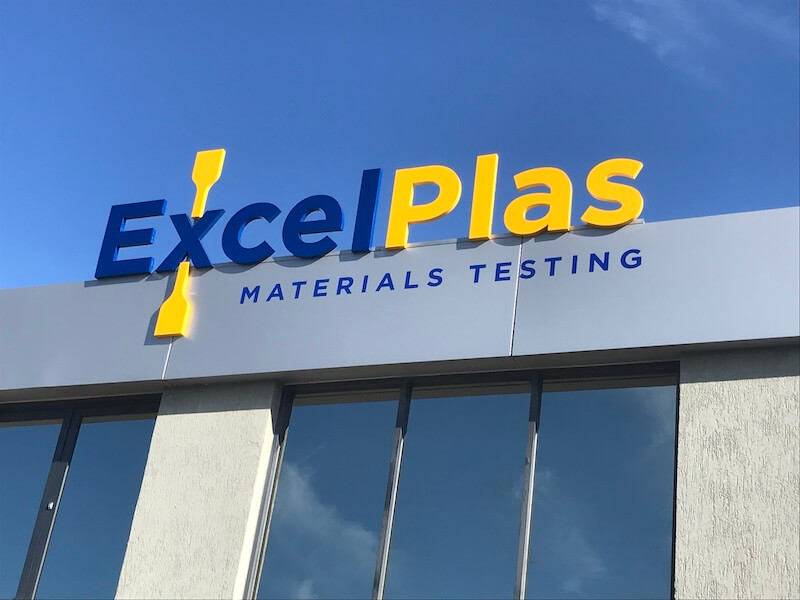
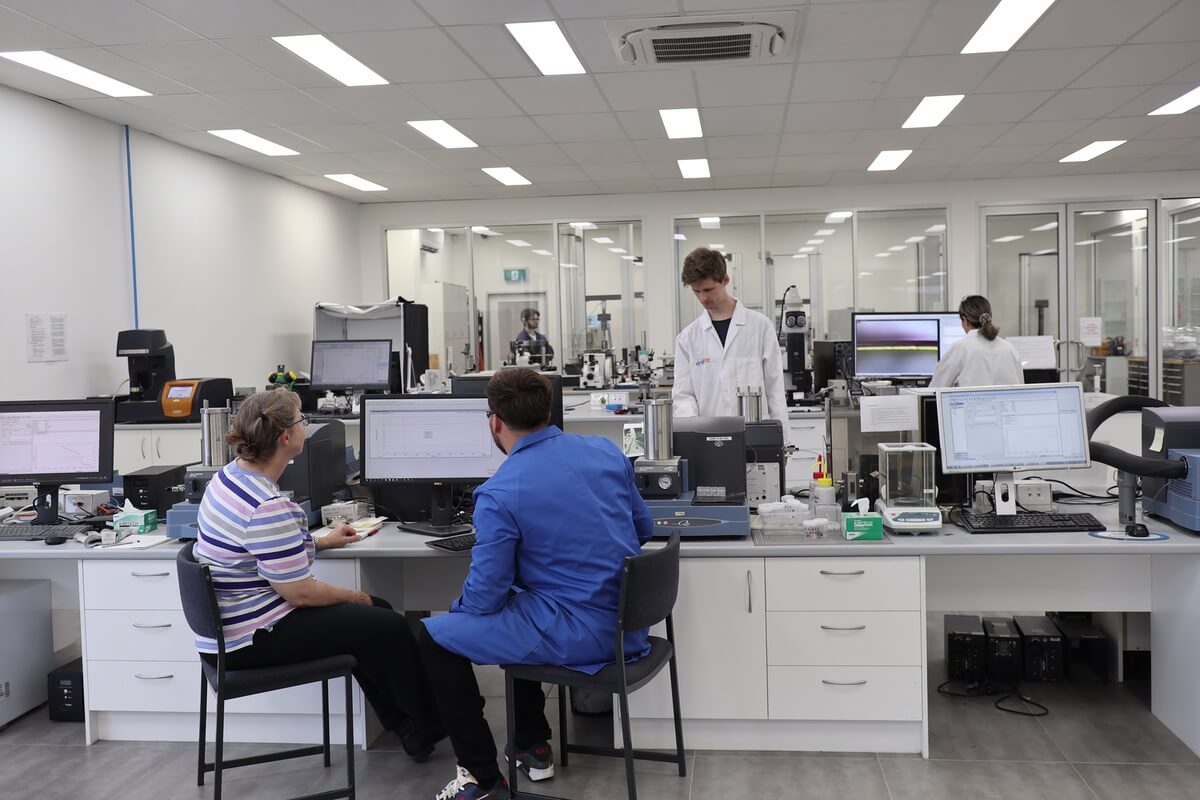