Geotextile Manufacturing – Continuous Filament vs. Staple Fibre: Unravelling Performance Differences
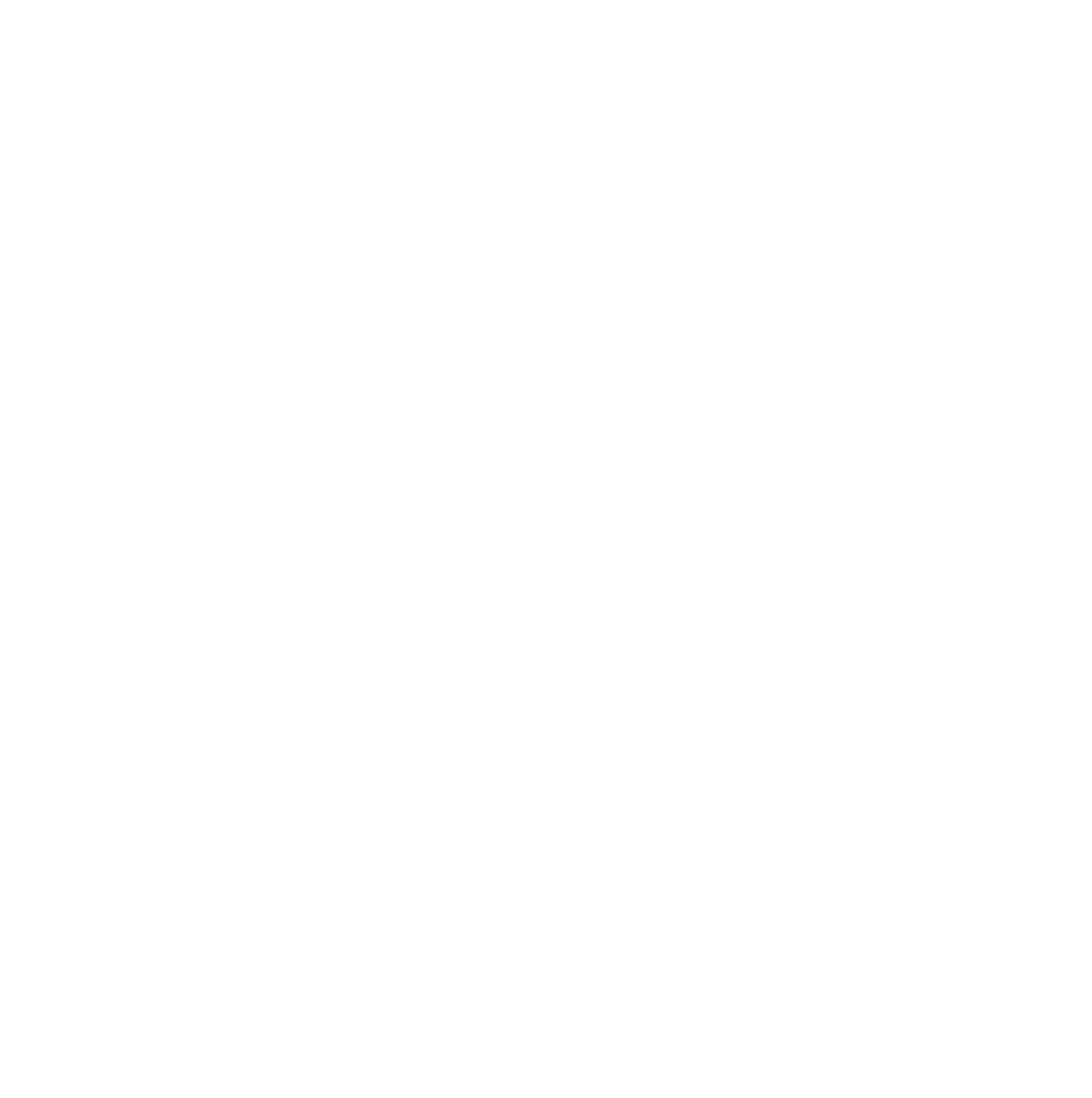
By GNA Editor
Opinion Pieces by Marc Amtsberg (Atarfil) and John Scheirs (ExcelPlas)
Marc has spent 20 years of working in the Geosynthetic sector as both a client and working with major manufacturers and he has observed an ongoing challenge across the industry. Marc has found that remains a general lack of focus on both the Geosynthetic Inputs and Manufacturing Processes that are so critical to product design life.
John has been testing polymers and geosynthetics for 30 years and he has pioneered some of the industry’s latest testing to evaluate long-term durability such as deformulation testing of additives in geosynthetics, thin-film accelerated immersion testing and the use of strain hardening modulus as a surrogate for the NCTL stress cracking resistance test.
An evaluation of the raw material and manufacturing process provide the key insight into expected Geosynthetic performance. Yet this is often overlooked in academic studies, in critical project testing, even for projects that require accountability in EPA regulations.
A reputable manufacturer will have extensive data and must be willing to identify their raw material supplier, their quality processes. If not willing to reveal their polymer inputs, demonstrated testing and project history then serious doubts should be raised over the suitability of their materials.
The fundamental challenge in using Geosynthetics, is short term testing on very small samples is being used to make performance assumptions for projects that can be millions of square metres. This assumption is only correct, if the product properties are replicated across every square metre. A designer who invests time to understand product inputs and manufacturing process, is better equipped to understand this project risk.
In this new GNA series, Marc and John document the most common technical questions encountered for common landfill and mining geosynthetic lining systems. Many of these properties are not measured by QC Testing, but nevertheless are critical in determining Geosynthetic product life.
Geotextile Manufacturing – Continuous Filament vs. Staple Fibre: Unravelling Performance Differences
Introduction
Geotextiles play a crucial role in various engineering projects, providing essential functions such as filtration, separation, reinforcement, and erosion control. Non-woven geotextiles are prevalent and can be manufactured using two distinct techniques: Continuous Filament (CF) and Staple Fibre (SF). Each method offers specific advantages and performance characteristics, making it essential to understand the differences between them for optimal selection in engineering applications. This article explores the manufacturing processes of CF and SF geotextiles and highlights their performance discrepancies that may not be adequately reflected in product datasheets.
Continuous Filament Geotextiles
Continuous Filament geotextiles are composed of long, unbroken strands of synthetic threads, which are laid together and then needled to enhance strength and stability. The continuous nature of the filaments results in a high tensile strength, making CF geotextiles exceptionally durable. Additionally, the absence of many fibre ends eliminates the risk of particle migration through the fabric, providing excellent filtration capabilities.
CF geotextiles are often preferred for projects that demand high strength and low elongation properties. These include applications such as road stabilization, embankment reinforcement, and erosion control in high-flow areas. Their smooth surface also ensures a low risk of clogging, making them suitable for drainage applications.
Staple Fibre Geotextiles
Staple Fibre geotextiles, on the other hand, consist of short fibres that are interlocked together, typically through a needling process. The resulting fabric construction offers improved abrasion resistance, making SF geotextiles suitable for applications involving stone movement, such as under rail tracks. However, staple fibres can also lead to potential drawbacks, such as increased direct damage factor and elongation risk in certain engineering conditions.
One common mistake is comparing CF to SF geotextiles solely based on product datasheets, as the mechanical properties differ significantly between the two. SF geotextiles are designed for specific engineering conditions, and their unique characteristics must be considered for accurate product selection.
Performance Differences and Considerations
When evaluating the performance of geotextiles, it is crucial to consider the manufacturing technique, as it directly influences the fabric's behaviour in various project functions. For example, the strain values at a given geotextile mass (e.g., 800 g/m2) indicate that CF geotextiles outperform SF geotextiles in limiting geomembrane strain. Additionally, the choice of polymer type can also influence cushioning performance.
As shown in Figure 1 below if the stain values for a given geotextile mass are compared, i.e. at 800 g/m2, it is apparent that continuous filament geotextiles performed better than staple fibre geotextiles at limiting geomembrane strain and additionally, polymer type influences cushioning performance as well.
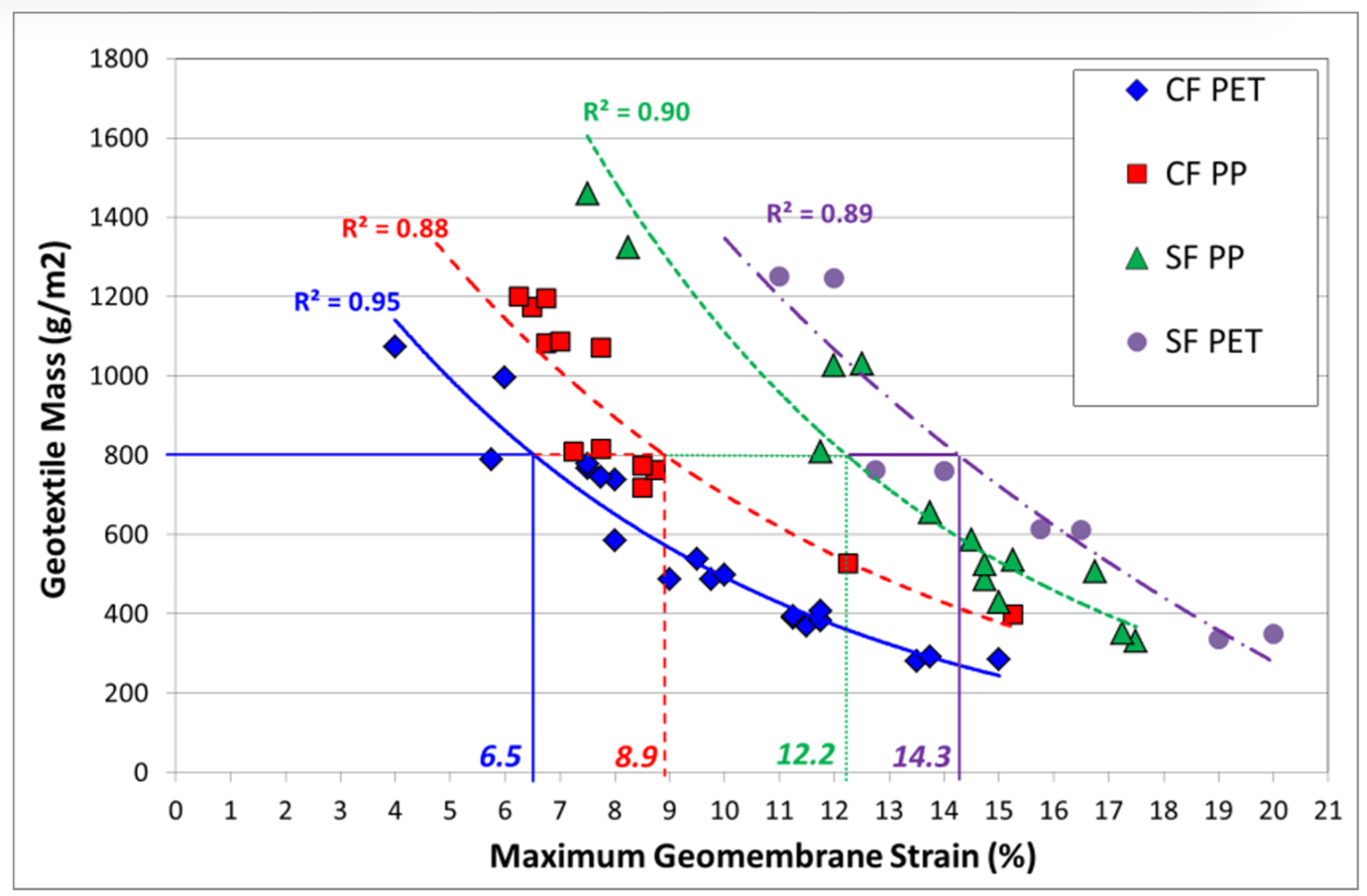
Manufacturing Technique Complexity
Beyond the broad categorization of CF and SF geotextiles, it is essential to recognize the wide range of performance differences within each category based on manufacturing techniques. For instance, thermal heat setting is commonly used to enhance the mechanical properties of SF geotextiles. However, improper implementation of this process can lead to compromised hydraulic performance and increased clogging risks.
Conclusions
In conclusion, geotextile manufacturing techniques, Continuous Filament, and Staple Fibre, each offer distinct advantages and disadvantages.
Proper selection of geotextiles for engineering projects requires a comprehensive understanding of their performance characteristics beyond what is available in product datasheets.
The direct link between manufacturing techniques and performance highlights the need for careful consideration of project requirements, strain limitations, and hydraulic performance to ensure the geotextile's optimal functionality.
Engineers, designers, and project managers must delve deeper into the specifics of geotextile manufacturing techniques to make informed decisions that align with the project's unique needs.
By recognizing the performance disparities between CF and SF geotextiles, stakeholders can optimize the success of various engineering applications and ultimately enhance the overall efficiency and longevity of their projects.
Take Home Message
Geotextile manufacturing technique has a direct link to performance for different project functions. This is not generally captured in product technical datasheets.
A common error is to compare a CF to a SF Geotextile across product datasheets, you will not observe the same mechanical properties. Staple Fibre Geotextiles are designed for specific engineering conditions that increase direct damage factor and elongation risk.
In terms of Geotextile manufacturing, broadly labelling them as Continuous Filament or Staple Fibre can also be misleading.
There is a vast range of performance differences according to manufacturing technique.
For SF, thermal heat setting which melts the geotextile surface is commonly done badly, and can improve the mechanical properties of the geotextile but lead to unacceptable loss of hydraulic performance and promote clogging.
References and More Reading
‘GEOMEMBRANE PROTECTION USING CUSHIONING GEOTEXTILES’
By R. A. Austin, Daniel T Gibbs and P. K. Kendall (2021).