Ensuring Geomembrane Performance: Unveiling the Secrets of HDPE and LLDPE Formulations
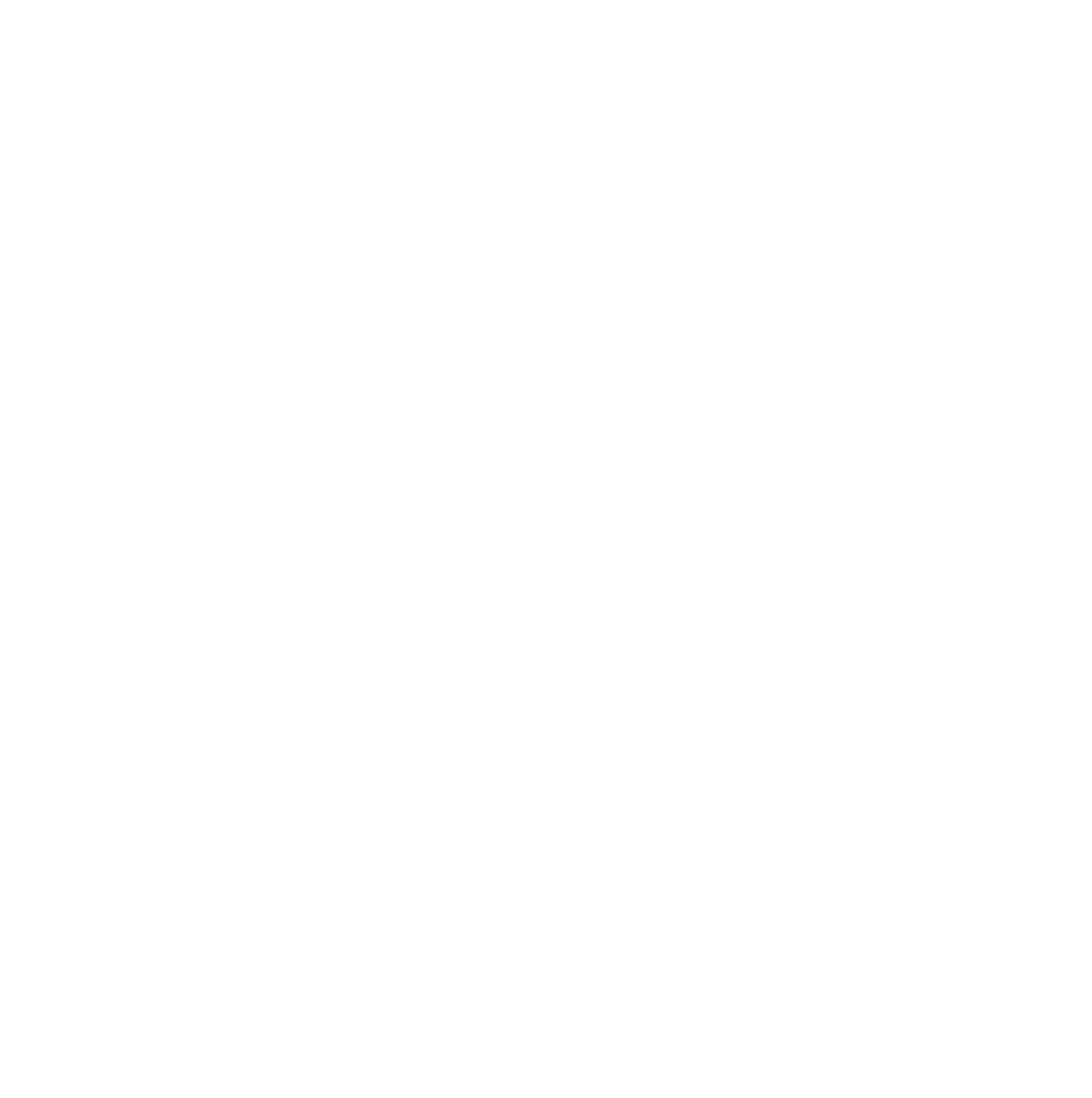
By GNA Editor
Opinion Pieces by Marc Amtsberg (Atarfil) and John Scheirs (ExcelPlas)
Marc has spent 20 years of working in the Geosynthetic sector as both a client and working with major manufacturers and he has observed an ongoing challenge across the industry. Marc has found that remains a general lack of focus on both the Geosynthetic Inputs and Manufacturing Processes that are so critical to product design life.
John has been testing polymers and geosynthetics for 30 years and he has pioneered some of the industry’s latest testing to evaluate long-term durability such as deformulation testing of additives in geosynthetics, thin-film accelerated immersion testing and the use of strain hardening modulus as a surrogate for the NCTL stress cracking resistance test.
An evaluation of the raw material and manufacturing process provide the key insight into expected Geosynthetic performance. Yet this is often overlooked in academic studies, in critical project testing, even for projects that require accountability in EPA regulations.
A reputable manufacturer will have extensive data and must be willing to identify their raw material supplier, their quality processes. If not willing to reveal their polymer inputs, demonstrated testing and project history then serious doubts should be raised over the suitability of their materials.
The fundamental challenge in using Geosynthetics, is short term testing on very small samples is being used to make performance assumptions for projects that can be millions of square metres. This assumption is only correct, if the product properties are replicated across every square metre. A designer who invests time to understand product inputs and manufacturing process, is better equipped to understand this project risk.
In this new GNA series, Marc and John document the most common technical questions encountered for common landfill and mining geosynthetic lining systems. Many of these properties are not measured by QC Testing, but nevertheless are critical in determining Geosynthetic product life.
Ensuring Geomembrane Performance: Unveiling the Secrets of HDPE and LLDPE Formulations
Abstract
Geomembranes play a vital role in modern engineering projects, offering impermeable barriers that protect the environment and infrastructure. However, the industry faces a challenge as manufacturers often keep their raw resin sources and formulations confidential, making it difficult to predict long-term performance accurately. This article discusses the potential of auditing geomembranes for critical projects without divulging specific ingredient details. Techniques like Deformulation testing using Nuclear Magnetic Resonance (NMR) and High-Performance Liquid Chromatography (HPLC) are explored to ensure consistency between tested and supplied geomembrane recipes. The article also emphasizes the importance of understanding both the resin source and formulation additives to guarantee the durability and reliability of geomembranes.
Introduction: The Geomembrane Challenge
Geomembranes, essential in civil engineering and environmental protection projects, face a significant challenge: manufacturers rarely disclose their raw material sources and formulations. This lack of transparency impedes accurate assessment of long-term performance and durability of geomembranes. However, there's an opportunity to audit geomembranes on critical projects without exposing proprietary details, ensuring consistency between tested samples and the delivered product.
Importance of Resin Type
The base resin makes up +97% of HDPE and LLDPE Geomembranes and is therefore the fundamental driver of behaviour long term but only measured with basic melt properties and finished sheet Stress Crack Resistance. Long-term Stress Cracking remains an industry blackspot when we consider site risk based on welding/handling, heat-affected zones and long-term wrinkling behaviour (particularly cycling temperature which generate cyclic stresses at the edge of the welds).
There is a vast range of geomembrane resins in the market, and a huge variance in performance under stress. Significant effort is spent understanding additive loss but once depleted, the resin type molecular weight and architecture predicts the risk long-term. A supplier should be able to demonstrate the quality of their resin through replicable long-term, Stress Crack Resistance (and Strain Hardening) analysis, as current industry guidelines do not capture this risk in short term (eg. GRI-GM13 500hrs for NCTL-SCR is well below good resin capability).
Unveiling the Resin Source: A Critical Step The foundation of geomembrane behaviour lies in its resin source, constituting over 97% of the material. This source determines long-term behaviour, stress-crack resistance, and welding performance. Currently, the industry guidelines lack comprehensive assessments of long-term stress-cracking risks and behaviour. Geomembrane manufacturers should be encouraged to disclose resin types and sources, as this information is vital for accurate risk assessment.
Deformulation Testing: A Solution for Recipe Consistency
One promising approach to address the transparency challenge is Deformulation testing, also known as reverse additive engineering. This technique employs advanced analytical methods like Nuclear Magnetic Resonance (NMR) and High-Performance Liquid Chromatography (HPLC) to quantify and analyze the components of geomembrane formulations. By comparing tested recipes to the supplied product, engineers can verify that the materials are consistent. This process becomes crucial in guaranteeing the intended performance of the geomembrane.
On multiple occasions, samples subjected to immersion testing, have not been the same recipe as the product delivered to site. This defeats the purpose of carrying out immersion testing and the supplier should bear this material risk.
Importance of Additive Selection and End-Use Environments
The formulation of geomembranes involves incorporating additives such as antioxidants and stabilizers to enhance production stability and long-term aging resistance. These additives are tested for property changes under various conditions, like elevated temperatures and oxygen exposure, simulating accelerated oxidation. The challenge arises when additives designed for superior performance in controlled conditions exhibit unforeseen vulnerabilities when subjected to real-world site conditions.
Mitigating Risk through Immersion TestinG
The risk factor for asset owners lies in the lack of application-specific immersion conditions during testing. While certain additives might show excellent performance in tests like High-Pressure Oxidation Induction Time (HPOIT) and Oxygen Induction Time (OIT) retention after Oven Aging, their resilience might diminish when exposed to specific chemical environments. For instance, some additives that perform well under oxygen exposure alone might become susceptible to deterioration when exposed to acidic or other corrosive media commonly use at mining sites.
Conclusions
In the realm of geomembranes, ensuring reliable and durable performance demands a multidimensional approach. By promoting transparency in resin source disclosure and encouraging comprehensive testing techniques, including Deformulation testing and immersion testing, the industry can bridge the gap between laboratory-controlled conditions and real-world challenges. This shift toward openness and meticulous evaluation will empower engineers, asset owners, and manufacturers to collaboratively develop geomembranes that excel in diverse environments and deliver on their promises of longevity and effectiveness.
14 Key Takeaways
- Manufacturing Transparency Challenge: One of the biggest hurdles in the geomembrane industry is the reluctance of manufacturers to disclose the raw resin source and formulation, which directly impacts the long-term performance of the product.
- Audit Opportunity: Despite the secrecy around formulations, there's a potential opportunity to audit geomembranes on important projects without needing to know the specific ingredients but rather the specific class of additives.
- Immersion Testing Mismatch: Immersion testing, a common practice to assess durability, has revealed that samples subjected to such tests may not match the actual product delivered to the site due to changes in formulation, leading to a disconnect between testing and real-world performance.
- Supplier's Responsibility: Manufacturers should be accountable for the material risk associated with discrepancies between tested samples and delivered products resulting from immersion testing.
- Deformulation Testing: Quantitative techniques like Nuclear Magnetic Resonance (NMR) and High-Performance Liquid Chromatography (HPLC) can be employed to reverse engineer the composition of geomembranes, ensuring that tested recipes align with the actual product used on-site.
- Additive Fit-for-Purpose: Deformulation testing not only validates recipe consistency but also ensures that additives selected for specific end-use service environments are appropriate and effective.
- Resin's Dominant Role: Resin source constitutes over 97% of HDPE and LLDPE geomembranes, making it a primary driver of long-term behaviour. However, its properties are often assessed only based on basic melt characteristics and stress crack resistance of the finished sheet.
- Long-Term Stress Cracking Challenge: The industry faces a challenge in predicting long-term stress cracking risks arising from factors like welding, handling, heat-affected zones, and temperature cycling, which can lead to complex behaviours in geomembranes.
- Varied Resin Performance: There's a wide range of geomembrane resins available in the market, and their performance under stress varies significantly, necessitating careful consideration during selection.
- Need for Comprehensive Assessment: To ensure geomembrane quality, manufacturers should go beyond basic resin properties and conduct replicable long-term stress crack resistance and strain hardening analyses, as current industry guidelines often lack comprehensive risk evaluation.
- Resin Source Disclosure: Geomembrane manufacturers should disclose the type of resin used and its country of origin to facilitate accurate assessment of the material's quality and behaviour.
- Formulation and Additives: Additives such as antioxidants and stabilizers are crucial for ensuring production stability and long-term aging resistance. Accelerated oxidation testing helps assess their effectiveness, but challenges arise when additives perform well in controlled conditions but fail in real-world site environments.
- Site Immersion Conditions: Immersion testing is vital to gauge how additives perform when exposed to actual site conditions, such as different chemical environments. It helps identify vulnerabilities that may not be apparent through other testing methods.
- Importance of Immersion Data: Geomembranes that pass High-Pressure Oxidation Induction Time (HPOIT) and Oxygen Induction Time (OIT) retention after Oven Aging tests may still experience rapid performance loss when subjected to certain chemicals on-site. Immersion data provides critical insights into real-world durability.