How to Prevent Failure of Epoxy Protective Coatings in LNG and Oil & Gas Asset Protection
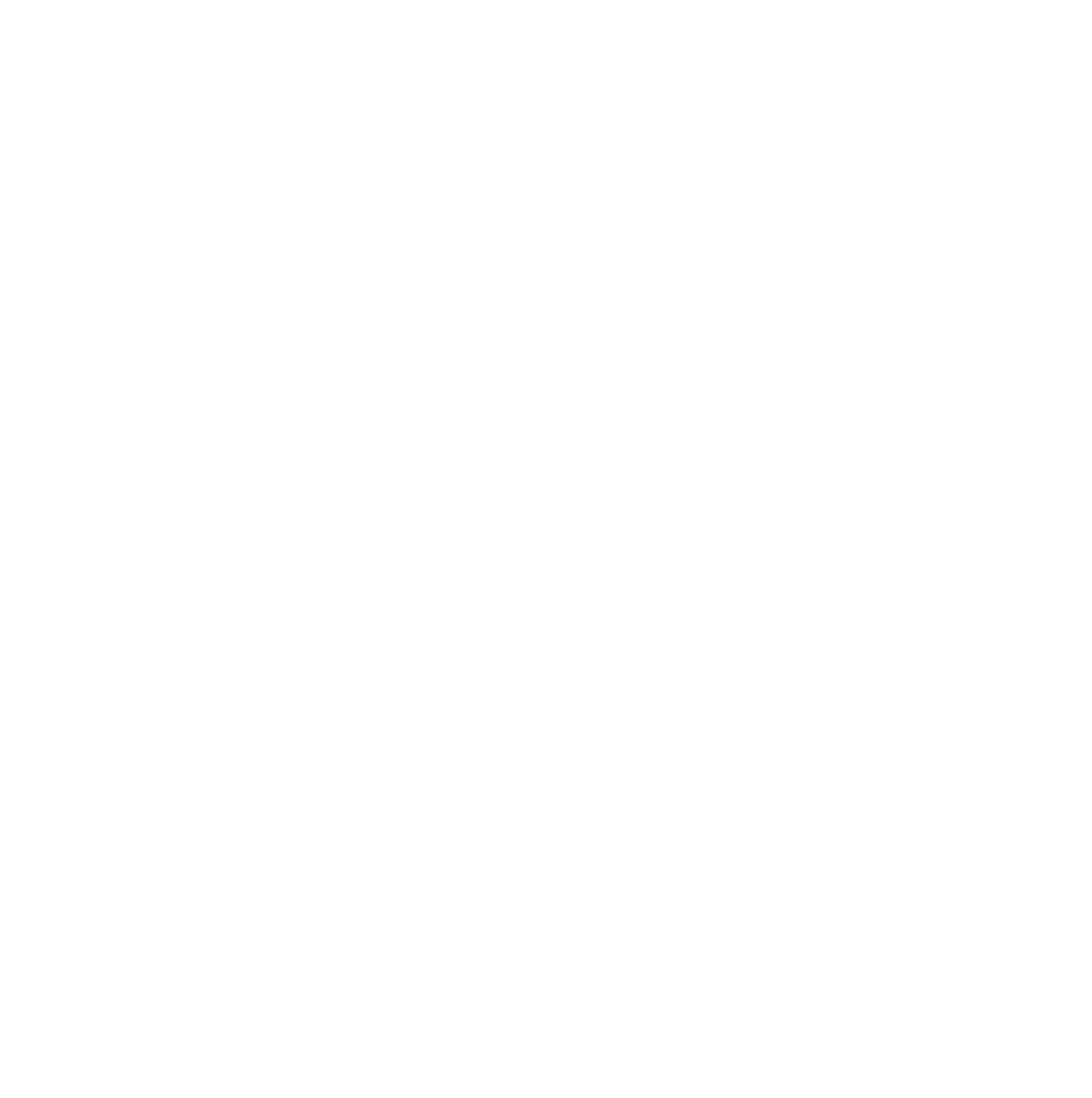
By PCN Editor
Introduction
Epoxy protective coatings play a crucial role in safeguarding LNG (liquefied natural gas) and oil and gas assets from the harsh environmental conditions they often face. However, the failure of these coatings can lead to significant financial and operational setbacks. To prevent such failures, ExcelPlas Coating Labs has outlined the following 12 simple rules for ensuring the effectiveness and longevity of epoxy protective coatings.
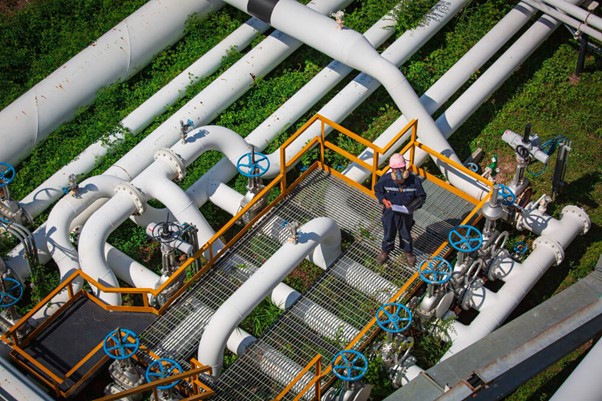
Rule #1 – Surface Cleanliness
Surface cleanliness is paramount when applying epoxy protective coatings. Substances like soluble salts, ion-specific contamination (such as sulphates, chlorides, and nitrates), and amine blush (for amine-cured epoxy coatings) can be invisible to the naked eye but can lead to premature coating failure. Therefore, it is essential to use appropriate test equipment to assess surface cleanliness before applying the coating.
Rule #2 – Climate, Dewpoint & Relative Humidity
Climatic conditions play a crucial role in coating application and performance. Monitoring factors like temperature, relative humidity, dewpoint, and moisture levels is vital. Dewpoint temperature (Td) is the point at which moisture forms on a surface due to condensation from the atmosphere. Calculating the difference in temperature (TΔ) between the surface temperature (Ts) and air temperature (Ta) helps determine when it's safe to apply the coating.
Rule #3 – Abrasive & Blast Inspection
During the abrasive or water jetting process, various parameters must be monitored, including air pressure, nozzle diameter, blast media contamination, and pH values to avoid recontamination of the substrate during blasting.
Rule #4 – Surface Condition Assessment
Assess the surface condition by evaluating factors such as the degree or percentage of rust and the level of mill scale. Pictorial Surface Standards can help visually assess surface conditions, while weld beads can be evaluated using a weld comparator and weld gauges.
Rule #5 – Surface Profile & Surface Roughness
The surface profile directly affects a coating's performance. It determines adhesion, coverage, and the overall volume of coating required. Both an excessive or insufficient profile can lead to issues. Surface roughness measurements involve using a stylus attached to an arm to record and measure roughness over a specified distance.
Rule #6 – Moisture Measurement
Moisture on the substrate can lead to poor adhesion, coating failure, and a compromised appearance. Ensure that the substrate is completely dry before applying epoxy coatings to prevent water vapour generation and coating damage.
Rule #7 – Wet Film Thickness
Measuring uncured film thickness helps determine the eventual dry film thickness. Applying the correct amount of coating is crucial to avoid issues such as cracking during curing or insufficient protection. Too much wet film can cause the coating to crack as it cures; too little coating increases the risk that the substrate will not be sufficiently protected, leading to rust spots.
Rule #8 – Oven Temperature Profile
Temperature profiling is essential during the curing process to measure the actual environmental and product temperature. Adjusting oven temperature settings based on the coated product's properties ensures a successful cure and consistent quality.
Rule #9 – Dry Film Thickness (DFT)
Dry Film Thickness is a critical measurement in the coatings industry, providing essential information about the coating's life expectancy, fitness for purpose, appearance, and compliance with international standards. Proper gauge usage is essential to meet coating inspection requirements. Over Coating: If too much coating is applied, as it cures internal stresses of the coating can cause it to crack. Under Coating: Uncoated areas, or where the coating flows away from edges or corners of a substrate or welds. Insufficient coating over a rough surface profile may also leave the peaks of the profile exposed.
Rule #10 – Data Acquisition and Analysis Software
Coating inspection generates a vast amount of data, including surface profile, cleanliness, climatic conditions, film thickness, and adhesion. Data management software can link directly with measurement devices to produce professional reports, ensuring compliance with relevant standards.
Rule #11 – Adhesion Testing
Adhesion testing quantifies the bond strength between the substrate and the coating or between different coating layers. Routine testing is essential for detecting potential coating failures early on, reducing the risk of rework and additional costs.
Rule #12 – Pinhole Detection
Flaws in the finished coating, such as pinholes, cissing (voids due to air bubbles), and cratering (voids due to poor flow characteristics), can lead to premature corrosion of the substrate. Vigilant pinhole detection by spark testing/holiday testing is necessary to prevent coating failures and subsequent asset damage.
Conclusions
In conclusion, adhering to these 12 rules provided by ExcelPlas Coating Labs can significantly enhance the performance and durability of epoxy protective coatings in LNG and oil and gas asset protection.By ensuring proper surface preparation, monitoring climatic conditions, and conducting thorough inspections, the risk of coating failures and their associated costs can be minimized, ultimately prolonging the life of critical assets in these industries.