Reducing Resin Costs: The Advantages of Physical Foaming for HDPE Pipe Manufacturers
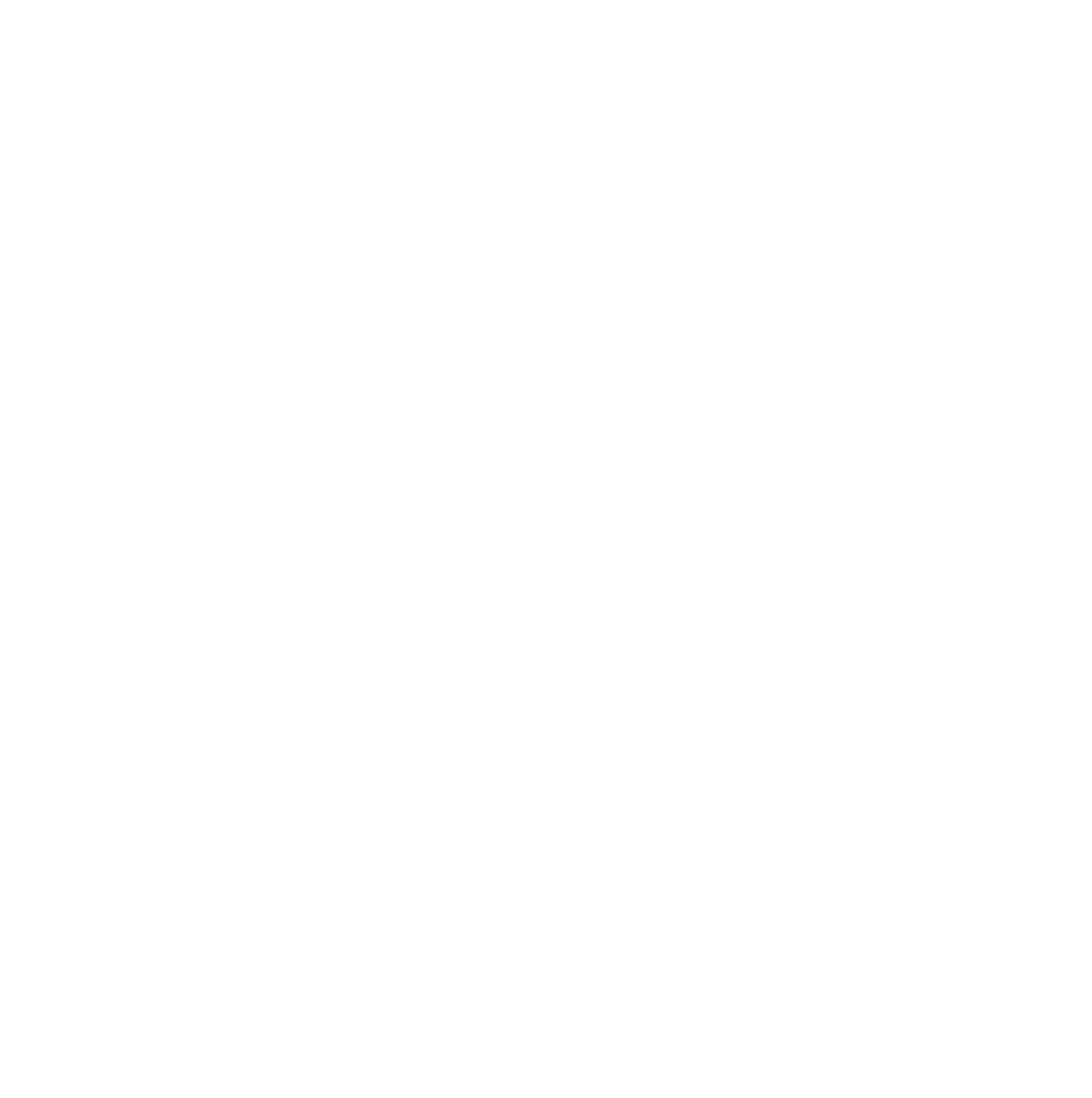
By PPN Editor
In the world of plastic pipe manufacturing, the quest to optimize costs without compromising quality is a perpetual challenge. As resin prices soar and material shortages persist, innovative solutions are crucial for maintaining competitiveness. One promising avenue for HDPE pipe makers to explore is the technique of physical foaming during the extrusion process.
What is Physical Foaming?
Physical foaming involves injecting gases such as carbon dioxide or nitrogen into the plastic before extrusion. This process creates a fine-pored foam within the pipe, reducing the amount of plastic needed while maintaining structural integrity. Unlike other foaming techniques that may involve substances of concern, physical foaming offers a more environmentally friendly approach with a smaller carbon footprint.
Collaborative Efforts Yield Promising Results
In a collaborative project between Hans Weber Maschinenfabrik GmbH and Promix Solutions AG, the feasibility and cost-saving potential of physical foaming were thoroughly evaluated. Hans Weber Maschinenfabrik GmbH, a renowned German company with a long history of expertise in mechanical engineering, provided the extrusion equipment necessary for the process. Meanwhile, Promix Solutions AG, based in Switzerland and specializing in mixing, foaming, and cooling products for plastics processing, contributed essential components for precise gas dosing and melt cooling.
Proven Benefits in Material Reduction
Initial trials utilizing Borealis' HDPE HE3490 Low Sag resin demonstrated significant material savings. By gradually increasing the gas injection, weight reductions of up to 26% for virgin material and approximately 15% for recycled material were achieved. These impressive results were attained while ensuring compliance with industry standards for pipe quality and performance.
Environmental Considerations and Sustainability
One of the key advantages of physical foaming is its alignment with sustainability goals. By reducing material consumption and avoiding the use of substances of concern, this technique offers a more environmentally conscious approach to pipe manufacturing. Additionally, the ability to incorporate recycled HDPE further enhances the sustainability profile of foamed pipes.
Navigating Challenges in a Dynamic Market
In today's dynamic market characterized by resin price fluctuations and material shortages, HDPE pipe manufacturers face mounting pressures to optimize costs. Physical foaming presents a viable strategy for mitigating these challenges, offering tangible benefits in both cost reduction and environmental impact. By embracing innovative solutions and collaborative partnerships, manufacturers can stay ahead of the curve and secure a competitive edge in the industry.
Conclusion
As the demand for plastic pipes continues to rise, the imperative to find cost-effective and sustainable manufacturing solutions becomes increasingly urgent. Physical foaming represents a promising avenue for HDPE pipe makers to reduce resin costs while minimizing environmental impact. Through collaborative efforts and innovative technologies, the industry can navigate the complexities of the market landscape and emerge stronger and more resilient than ever before.