The Future of Geomembrane Welding
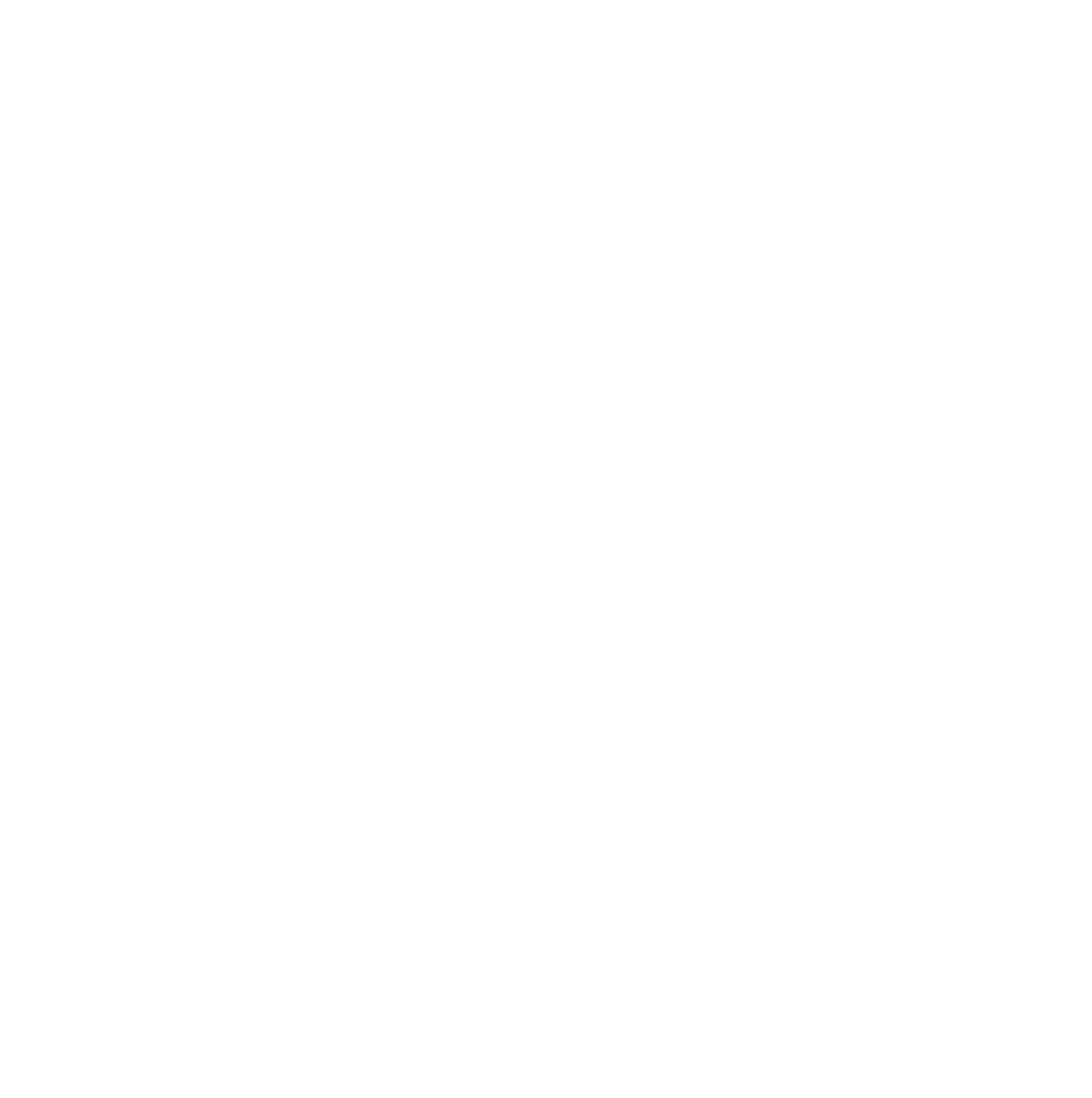
By GNA Editor
What does the near future hold for geomembrane liner welding?Well certainly heated brass wedges which rely of electrical resistance heaters and the poor thermal conductivity of PE is not the future.A teaser video was released by Swiss Company GF for welding of PE pipes by Infra-red Radiation <https://www.youtube.com/watch?v=s9gXxy8aKjc> is prescient and could hold the answer.Since the geomembrane industry usually adopts new developments in the plastic pipe field some 5-10 years later such as the use of PERT resins and EVOH barriers it is highly likely that geomembrane welding will follow this trend.
The Dawn of a New Era in Geomembrane Liner Welding
The realm of geomembrane liner welding stands on the cusp of a profound evolution, driven by the advent of pioneering techniques such as Infrared (IR) welding. Traditional methods, typified by the use of heated brass wedges, are gradually yielding ground, their limitations in efficiency and efficacy becoming increasingly apparent, especially when dealing with materials like HDPE that exhibit very poor thermal conductivity.
A tantalizing glimpse into this forthcoming transformation was recently unveiled through a teaser video by Swiss Company GF, unveiling the application of IR radiation for welding PE pipes. This ground-breaking approach harnesses a spectrum of wavelengths from the electromagnetic spectrum to heat and weld plastic components, presenting a beacon of promise for the geomembrane industry.
The advantages bestowed by IR welding upon geomembranes are manifold. Its hallmark precision enables meticulous control over the welding zone, yielding visually impeccable weld seams adorned with consistent air channels and symmetrical squeeze-outs. Moreover, the technique facilitates tighter tolerances in the fusion process owing to its uniform heating, resulting in a diminished Heat Affected Zone and enhanced weld quality characterized by deeper and more uniform heat penetration.
In contrast to conventional welding methodologies, IR welding boasts accelerated heating and cycle times, ensuring heightened productivity and quality even amidst adverse conditions such as cold weather, where heat loss due to frigid winds poses a challenge. Furthermore, the absence of direct contact between heating elements and plastic components in IR welding circumvents issues like the carbonization of brass wedge blocks, thus averting potential voids in the welded seams from the evolution of volatiles and degradation products.
Furthermore, the integration of IR receptor additives into HDPE sheets holds promise for further optimization of the welding process by augmenting the absorption of IR radiation. Given the geomembrane industry's historical proclivity for embracing innovations from the plastic pipe sector, the ascent of IR welding within geomembrane applications appears imminent, heralding a paradigm shift in the fabrication and installation of liners.
IR welding typically uses a range of wavelengths from 800 to 11,000 nm on the electromagnetic spectrum to heat, melt, and fuse the interface between two plastic parts through the absorption and conversion of the IR energy into heat.The advantages of IR welding of geomembrane are many such as:
- Precise control of the welding zone
- Aesthetically pleasing weld seams – visually OK with consistent air channels and symmetrical squeeze-outs
- Ability to achieve tighter tolerances in the fusion process due to more uniform heating
- A lower Heat Affected Zone
- Drastically improved weld quality due to deeper and more uniform heat penetration
- Fast heating and cycle time than other conventional geomembrane welding processes.
- Ensures higher productivity and quality in cold weather welding
- Lowers heat losses by cold winds
- Non-contact heating on the weld interface prevents plastic parts from sticking to the hot wedges and degrading (no more carbonization of the brass wedge blocks and vapours potentially leading to voids.
- The ability to add IR receptor additives to the HDPE sheet to increase the absorption of the IR radiation.
Conclusions
The future of geomembrane liner welding is poised for a significant transformation, with the adoption of the innovative technique of Infrared welding (IRW) leading the way. Traditional methods, like heated brass wedges, will likely be gradually being phased out due to limitations in efficiency and effectiveness, particularly with materials like HDPE that have very poor thermal conductivity.
A glimpse into this future was provided by a teaser video released by Swiss Company GF, showcasing the welding of HDPE pipes using IR radiation. This method, which utilizes a range of IR wavelengths on the electromagnetic spectrum to heat and fuse plastic parts, holds great promise for the geomembrane industry.
The advantages of IR welding for geomembranes are numerous. Firstly, it offers precise control over the welding zone, resulting in aesthetically pleasing weld seams with consistent air channels and symmetrical squeeze-outs. Additionally, IR welding enables tighter tolerances in the fusion process due to more uniform heating, resulting in a lower Heat Affected Zone and improved weld quality with deeper and more uniform heat penetration.
Compared to conventional geomembrane welding processes, IR welding boasts faster heating and faster seaming times, ensuring higher productivity and quality even in cold weather conditions where heat loss by cold wind is a concern. Furthermore, the non-contact heating characteristic of IR welding prevents plastic parts from sticking to hot wedges, eliminating issues like carbonization of brass wedge blocks and potential voids.
Moreover, IR receptor additives can be incorporated into HDPE sheets to enhance the absorption of IR radiation, further optimizing the welding process. Given the geomembrane industry's tendency to adopt advancements from the plastic pipe field, it's highly likely that IR welding will gain traction in geomembrane applications within the next 5-10 years, revolutionizing the way liners are fabricated and installed.